How 5D BIM Can Shake Up the Construction Industry
- Michael McCarthy
- Sep 5, 2017
- 3 min read
Updated: Aug 20, 2020
The construction industry is over-due for a massive shake up. While other industries have seen productivity increases and costs fall, construction has seen the opposite.

Productivity has fallen and costs have risen. In reality, this could be attributed to increased building and safety regulations. The industry has not managed to find productivity savings to counter balance these necessary improvements in quality and safety.
The traditional model of construction has relied on a hard core of seasoned subcontractors employing manual labour on site to deliver projects.
The design process has been not much better, separate consultants designing separately and figuring out any problems on site as they arise in the hope that it will be all-right at the end. This has lead in the past to extras, conflicts and delays to the inevitable expense of clients.
This decentralised approach to design and construction has brought us to where we are today: an industry that is mired in low profitability, high litigiousness, inconsistent quality and short supply.
It’s over due time for a change. In 2016 McKinsey, a consultancy, produced a report entitled ‘Imagining Construction’s Digital Future’ and has highlighted this.
One particular area it has identified is the application of 5D BIM. This is where costs are managed using the BIM model. We are at the very early stages of this concept at the moment.
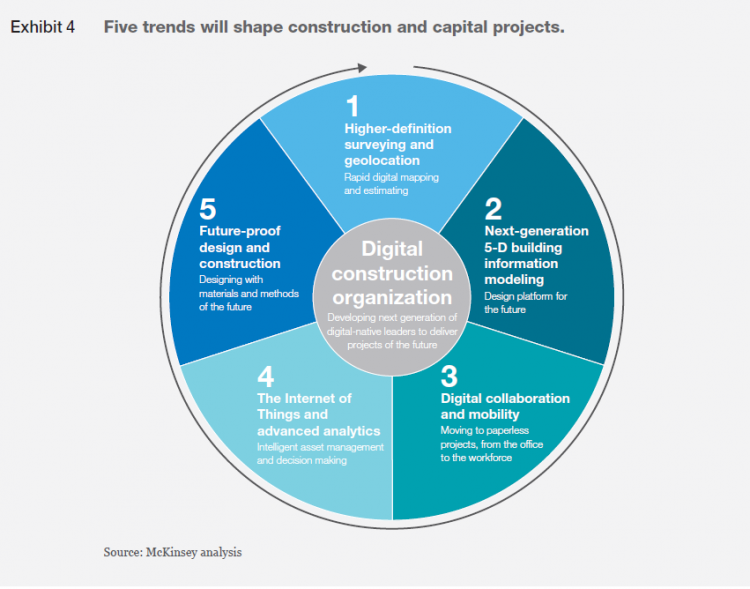
However, technology is one of the lesser hurdles. The main obstacle is mindset. The current ‘silo’ approach to design leads to inefficiency. A more open and collaborative mindset is required in order to move towards a 5D BIM world.
We are currently a long way off. Of the UK projects we have been involved with, about 50% of the projects with a BIM model have made it available with the tender documentation. Of the remaining 50%, about half of those made it available after request. The other 25% refused to make it available at all.
In Ireland, our experience has been that BIM models are far less common, or are shared considerably less.
The Promise of 5D BIM
BIM brings the promise of resolving these manifold problems. By developing one central model, designers can add their design to a single 3D model. This has the benefit of resolving any clashes as they are designed and by making elements of the design suitable for automated manufacture.
The power of BIM is nowhere near being realised. A significant, and as yet untapped, benefit lies in the using it for cost management, which is what the 5D prefix is intended to signify.
Currently, cost management is predominately a paper based or 2D exercise requiring the manual taking off of quantities from paper or on-screen PDF drawings. These are then worked into an estimate using particular sets of rules.
This is an incredibly labour intensive approach to cost management.
What can be done with 5D BIM consigns this approach to the waste paper basket. Rapid production of detailed digital estimates to give 100% accurate information in a fraction of the time of the manual based systems. This allows designers to be informed of the cost effect of their design choices as they arise. This will save considerable time on the design process as well as saving clients considerable sums and lost time.
Saving time in the preparation of estimates is just the low hanging fruit. The real value comes in the form of cost analysis, research and development of supply chain efficiencies that BIM enables.
What’s more, BIM for cost management can occur at the early stages of the model development as model components can be manipulated to compensate for undeveloped information.
At MMC Quantity Surveyors, we are at the leading edge of using BIM for cost management. We have seen and used its potential for several years now.
We are actively looking for designers and clients to collaborate with it to help realise the savings and efficiencies this platform can help realise.
If this is of interest to you, please call us to find out more.
See here for more information https://mmcqs.com/services/bim-5d-estimating/
Comments